Porosity in Welding: Identifying Common Issues and Implementing Best Practices for Prevention
Porosity in welding is a prevalent problem that frequently goes unnoticed till it triggers significant problems with the stability of welds. In this conversation, we will discover the essential variables contributing to porosity formation, analyze its damaging impacts on weld performance, and review the ideal methods that can be adopted to minimize porosity occurrence in welding procedures.
Typical Sources Of Porosity
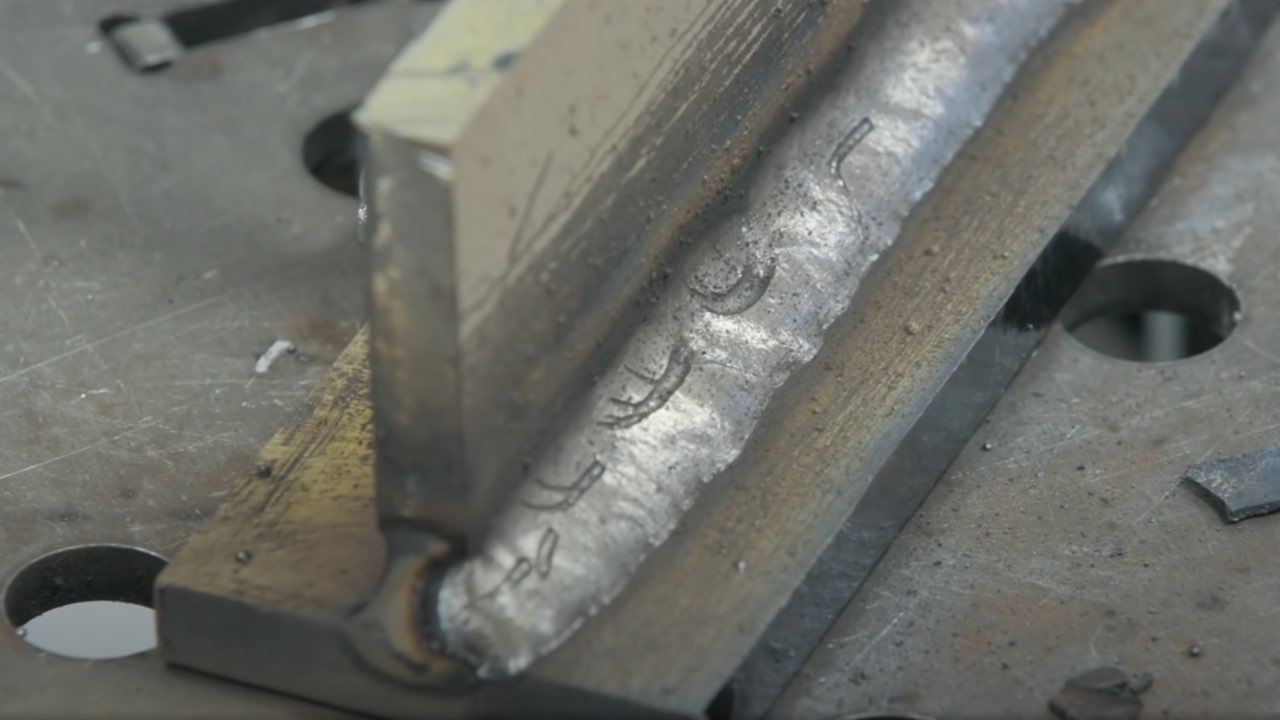
Another constant perpetrator behind porosity is the visibility of contaminants on the surface of the base steel, such as oil, oil, or corrosion. When these contaminants are not properly removed prior to welding, they can evaporate and come to be trapped in the weld, triggering problems. Moreover, making use of filthy or damp filler materials can present contaminations right into the weld, adding to porosity problems. To alleviate these typical causes of porosity, extensive cleaning of base metals, appropriate protecting gas choice, and adherence to ideal welding criteria are crucial practices in achieving top quality, porosity-free welds.
Influence of Porosity on Weld Top Quality

The existence of porosity in welding can significantly endanger the structural honesty and mechanical buildings of bonded joints. Porosity creates spaces within the weld steel, damaging its overall toughness and load-bearing capability.
Among the key repercussions of porosity is a decrease in the weld's ductility and sturdiness. Welds with high porosity degrees often tend to exhibit lower influence stamina and lowered ability to deform plastically before fracturing. This can be specifically worrying in applications where the bonded components are subjected to dynamic or cyclic loading conditions. Additionally, porosity can hamper the weld's capability to successfully send forces, bring about early weld failing and possible security threats in crucial frameworks.
Best Practices for Porosity Prevention
To enhance the architectural integrity and top quality of welded joints, what details procedures can be implemented to decrease the occurrence of porosity throughout the welding process? Making use of the appropriate welding strategy for the particular product being welded, such as changing the welding angle and gun setting, can better avoid porosity. Routine assessment of welds and prompt removal of any kind of issues determined throughout the welding process are vital techniques to avoid porosity and generate top quality welds.
Value of Proper Welding Methods
Applying proper view it welding methods is extremely important in guaranteeing the architectural honesty and quality of welded joints, constructing upon the foundation of efficient porosity avoidance measures. Welding techniques directly affect the total toughness and resilience of the welded framework. One vital facet of appropriate welding methods is maintaining the proper warmth input. Excessive heat can lead to increased porosity as a result of the entrapment of gases in the weld pool. On the other hand, not enough warmth might cause incomplete fusion, creating prospective powerlessness in the joint. In addition, making use of the ideal welding criteria, such as voltage, current, and travel speed, is important for accomplishing audio welds with marginal porosity.
Additionally, the selection of welding procedure, whether it be MIG, TIG, or stick welding, should align with the particular demands of the task to make certain ideal results. Proper cleansing and preparation of the base steel, as well as selecting the best filler material, are also important elements of skillful welding techniques. By adhering to these best practices, welders can minimize the risk of porosity formation and Web Site produce premium, structurally sound welds.

Testing and Quality Assurance Measures
Testing treatments are vital to detect and avoid porosity in welding, guaranteeing the stamina and toughness of the final item. Non-destructive screening techniques such as ultrasonic testing, radiographic screening, and aesthetic examination are generally utilized to determine potential defects like porosity.
Post-weld assessments, on the other hand, assess the last weld for any kind of defects, including porosity, and verify that it fulfills specified standards. Carrying out a thorough quality control plan that includes complete screening treatments and assessments is critical to reducing porosity concerns and guaranteeing the overall top quality of welded joints.
Verdict
Finally, porosity in welding can be an usual concern that influences the quality of welds. By identifying the review common root causes of porosity and executing finest methods for prevention, such as appropriate welding methods and testing procedures, welders can make sure high top quality and trustworthy welds. It is vital to focus on avoidance approaches to decrease the event of porosity and preserve the stability of welded structures.